Went through the data again, this time comparing to a test day with much cooler weather. Logs used:
Colder weather (two radiators in series, two large oil coolers, nonHD 7in FMIC, poor ducting and insulation from radiator, 100% coolant):
datazap.me
Log from three days ago:
datazap.me
Current | Previous (two radiators in series only) | |
| Session 1 | Session 2 |
110F ambient, 1:36-ish laps | 84F ambient (cluster), 1:40-ish laps | 84F ambient (cluster), 1:40-ish laps |
iat min 115F (46C),
peak oil 280F (138C), 170F over ambient
time to -10F oil from peak: 100s, coasting
time from 208F to 232F (+24F) coolant: 109s
peak iat 212F (102F over ambient) | iat min 93F (34C),
peak oil 268F (131C), 184F over ambient
time to -10F oil from peak: 100s, coasting
time from 187F to 223F (+36F) coolant:104s
peak iat 165F (81F over ambient) | iat min 95F (35C),
peak oil 273F (134C), 189F over ambient
time to -10F oil: 110s, coasting
time from 205F to 228F (+23F) coolant: 104s
peak iat 162F (78F over ambient) |
So my conclusions here are
1) With the 7.5in HD custom FMIC, better ducting and insulation from radiators, iats do in fact get closer to ambient when coasting.
2) Peak iats over ambient were higher. I take this as evidence that I was pushing harder. This is supported by the lap times. BTW I also note that third gear pulls are pretty useless at evaluating actual FMIC performance on track, see *) below
3) Although the oil pan oil cooler is now covered by an aux radiator, peak oil over ambient doesn't seem to suffer. The rate at which the oil cools also doesn't seem to suffer. This was my biggest concern with the new setup.
4) Although pushing harder, and doing so in much hotter weather, the rate of temperature increase for coolant was actually slightly better.
5) Coolant increasing from 208F to 232F (+24F) in 109s is still unacceptable for any type of endurance competition, but it has to be compared to when I was running CSF only: From 219F to 248F (+29F) in 106s (100F ambient). Even the previous setup would take twice as long to "achieve"
that.
*) When FMIC cold, iat doesn't increase from start to end of a 3rd gear pull:
datazap.me
When FMIC is a bit heat soaked, iat actually decreases during a 3rd gear pull:
datazap.me
None of this means that iats can't go as high as 212F later. In fact it did within the very same log. The above pulls were done before and after the track "session" while still on track:
datazap.me
Next steps
I'm convinced coolant cooling is still where efforts need to be placed. I am also convinced that the combination of aux radiators with booster pump is effective on this car. The fact that the N55 M2 uses a booster pump and the M2C + new S58 with larger radiators don't, tells me that the N5x electric coolant pump was found to be a weak link after adding an aux radiator.
I have ordered the 120W (3600l/h) version of the booster pump I installed as a first easy upgrade. Lets see if that makes a difference.
I am also considering making some air pressure measurements with and without the under tray. Perhaps it would be beneficial to make a custom under tray in aluminum with large outlets behind the fmic/fan and aux coolers. But it is my general belief that since no major air flow changes were made between the M2 and M2C, that this is not really where time needs to be invested. However it needs to be noted that the M2C does indeed have an outlet for its oil cooler behind the bumper.
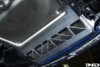